Comprehending the Fundamentals and Applications of Plastic Extrusion in Modern Manufacturing
In the realm of contemporary production, the technique of plastic extrusion plays a critical role - plastic extrusion. This detailed process, involving the melting and shaping of plastic with specialized passes away, is leveraged throughout numerous sectors for the creation of diverse items. From car components to durable goods packaging, the applications are vast, and the potential for sustainability is similarly remarkable. Deciphering the basics of this procedure reveals truth flexibility and capacity of plastic extrusion.
The Principles of Plastic Extrusion Process
While it may show up complicated, the basics of the plastic extrusion process are based on reasonably uncomplicated concepts. It is a manufacturing procedure where plastic is melted and after that shaped right into a continuous profile with a die. The plastic extrusion procedure is thoroughly utilized in different industries due to its cost-effectiveness, efficiency, and convenience.
Different Kinds Of Plastic Extrusion Techniques
Structure upon the basic understanding of the plastic extrusion process, it is essential to explore the different strategies associated with this manufacturing approach. Both primary strategies are profile extrusion and sheet extrusion. In profile extrusion, plastic is melted and developed right into a constant account, typically used to produce pipes, poles, rails, and home window frames. In comparison, sheet extrusion develops huge, flat sheets of plastic, which are normally more refined right into products such as food packaging, shower curtains, and car components. Each technique requires specialized equipment and accurate control over temperature level and stress to make certain the plastic preserves its shape during cooling. Comprehending these techniques is essential to utilizing plastic extrusion efficiently in contemporary manufacturing.
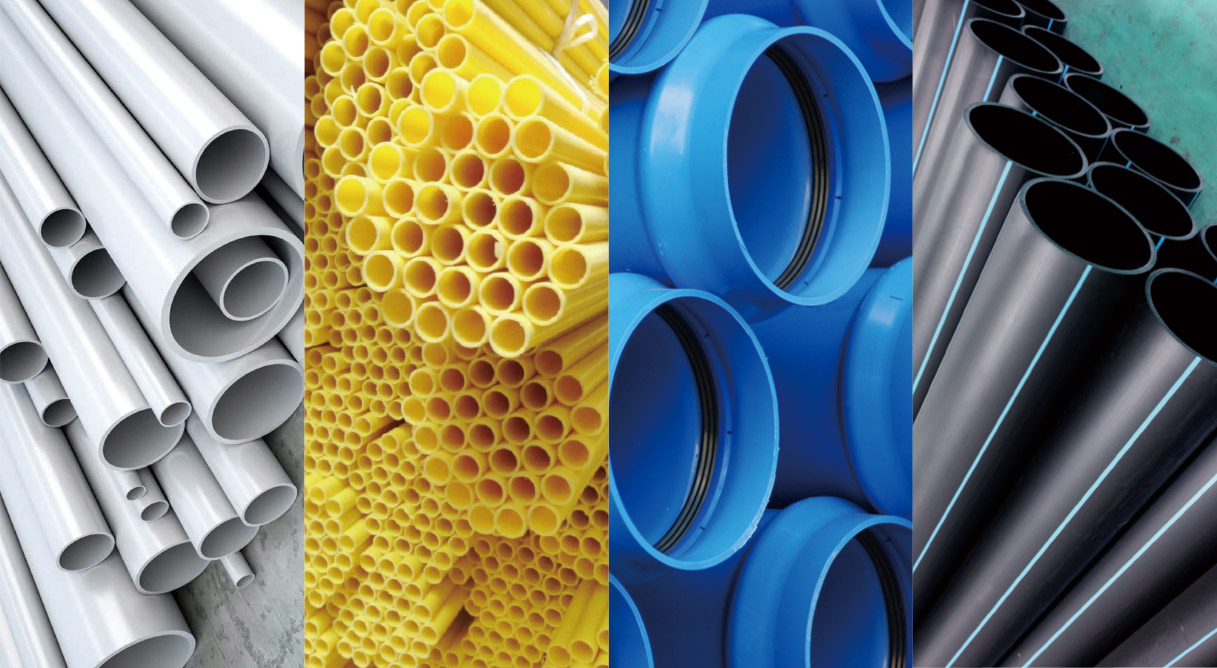
The Function of Plastic Extrusion in the Automotive Industry
An overwhelming bulk of parts in contemporary lorries are items of the plastic extrusion procedure. This procedure has transformed the automobile industry, changing it into a more effective, cost-effective, and flexible manufacturing market. Plastic extrusion is largely utilized in the production of different automobile components such as bumpers, grills, door panels, and dashboard trim. The process provides an attire, consistent output, allowing makers to browse around this site generate high-volume components with great accuracy and minimal waste. The lightness of the extruded plastic components adds to the overall reduction in lorry weight, boosting gas effectiveness. Additionally, the longevity and resistance of these parts to warmth, cool, and influence enhance the long life of automobiles. Thus, plastic extrusion plays a pivotal role in vehicle production.

Applications of Plastic Extrusion in Consumer Goods Production
Beyond its considerable influence on the automobile sector, plastic extrusion proves just as efficient in the world of customer goods making. This procedure is vital in creating a vast range of products, from food product packaging to household appliances, playthings, and also medical tools. The adaptability of plastic extrusion permits suppliers to develop and generate complicated shapes and sizes with high accuracy and efficiency. In addition, due to the recyclability of several plastics, extruded components can be reprocessed, lowering waste and cost. The flexibility, flexibility, and cost-effectiveness of plastic extrusion make it a preferred option for numerous durable goods suppliers, adding significantly to the market's development and advancement. However, the environmental ramifications of this extensive use need careful visit this web-site consideration, a topic to be reviewed even more in the succeeding area.
Ecological Influence and Sustainability in Plastic Extrusion
The prevalent usage of plastic extrusion in producing welcomes examination of its environmental implications. Efficient machinery minimizes energy use, while waste monitoring systems reuse scrap plastic, decreasing raw product needs. Despite these renovations, further innovation is required to alleviate the environmental footprint of plastic extrusion.
Conclusion
In final thought, plastic extrusion plays an essential function in modern production, especially in the automobile and customer items sectors. Recognizing the fundamentals of this procedure is essential to maximizing its advantages and applications.
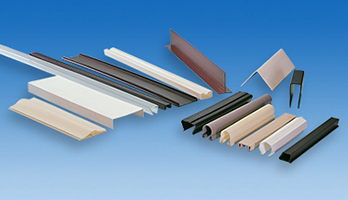
The plastic extrusion process is extensively utilized in numerous markets due to its flexibility, efficiency, and cost-effectiveness.
Structure upon the standard understanding of the plastic extrusion process, it is needed to explore the various techniques involved in this manufacturing method. plastic extrusion. In contrast, sheet extrusion develops huge, flat sheets of plastic, which are generally more processed into products such as food product packaging, shower drapes, and auto parts.An overwhelming majority of components in modern cars are products of the plastic extrusion procedure